Publi-information ~
En 2025, les technologies numériques vont continuer à remodeler l’industrie manufacturière. En fait, selon le Deloitte Research Center for Energy & Industrials, 83 % des industriels pensent qu’au cours des cinq prochaines années les solutions numériques vont révolutionner la façon dont les produits sont fabriqués. En effet, leurs avantages potentiels incluent des gains importants en matière d’utilisation efficiente des ressources, de productivité de la main-d’œuvre et de qualité des produits, ainsi que des réductions de coûts et des progrès en matière de sécurité et d’écoresponsabilité.
Nous constatons déjà une augmentation du nombre d’entreprises – des start-up et des petits ateliers jusqu’aux grands constructeurs – qui recourent à la numérisation pour simuler et optimiser leurs produits et leurs processus avant même de construire une nouvelle usine. Ensuite, une fois l’usine en service, ces entreprises peuvent exploiter les données de fabrication complètes qu’elles y collectent pour anticiper les changements et affiner les flux de production. En outre, elles peuvent s’appuyer sur la transformation numérique pour optimiser la production tout en renforçant leur écoresponsabilité, assurant ainsi leur avenir dans le secteur manufacturier. Travaillant dans ce secteur depuis 40 ans, je suis impatient de voir comment ces transformations vont redéfinir le champ des possibles dans le domaine de la fabrication.
La continuité numérique, pilier de la transformation numérique
Dans le monde entier, de nombreuses entreprises ont adopté des outils de CAO pour numériser la conception de leurs produits au cours de leur développement. Mais peu d’entre elles exploitent les possibilités qu’offre la transformation numérique pour la planification de la fabrication et, plus tard, pour la production et son optimisation, la logistique, la chaîne d’approvisionnement et la gestion de l’entretien des produits en cours d’utilisation. Par conséquent, la numérisation de la fabrication et la planification des sites de production sont des domaines-clés sur lesquels nous devons faire porter tous nos efforts pour pouvoir devenir beaucoup plus performants, efficients, résilients et agiles.
En adoptant une stratégie globale de numérisation, les industriels peuvent définir numériquement des flux de travail entiers, permettant ainsi une collaboration fluide entre la conception, l’ingénierie et la fabrication. Leurs produits peuvent alors être conçus, simulés et fabriqués dans le monde numérique avant de l’être dans le monde réel. Cette stratégie peut aussi permettre d’exploiter encore plus les installations de production, ce qui passe par une automatisation accrue, l’utilisation d’un plus grand nombre de robots, et davantage d’opérations et d’opérateurs intelligents épaulés par l’informatique dématérialisée (cloud computing) et l’intelligence artificielle (IA). La fabrication numérique a déjà été adoptée par de nombreux secteurs, notamment l’automobile, l’aéronautique, l’électronique et la santé.
Les continuités numériques sont des chaînes de solutions construites à partir de différents produits. Ces produits doivent être correctement connectés pour pouvoir fonctionner ensemble. Le client sait la valeur qu’offre cette chaîne de bout en bout, mais il n’a pas nécessairement besoin de mettre en œuvre la totalité de la chaîne. Il est important d’offrir de la souplesse pour lui permettre d’adapter l’outil à ses besoins spécifiques. Par exemple, un industriel peut commencer par choisir une solution unique, telle qu’un logiciel de CAO/FAO, puis passer au niveau supérieur afin de créer une continuité numérique de bout en bout. Mais il a besoin de savoir que tous ces composants vont fonctionner ensemble dans la continuité numérique, permettant à l’information de circuler entre le bureau d’études et l’usine et vice-versa.
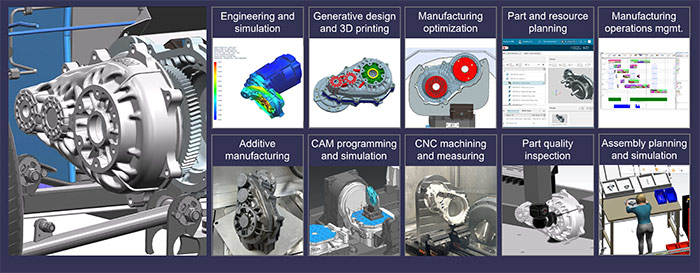
Par exemple, Siemens a créé un jumeau numérique complet de son usine de moteurs et de transmissions de Nanjing (Chine), ce qui a permis d’effectuer une analyse approfondie dans le monde numérique avant tout investissement réel. En simulant divers scénarios – tels que les interactions entre les robots, les véhicules autoguidés et les humains – afin d’optimiser les processus dans l’environnement virtuel, Siemens a pu réduire les coûts et s’assurer que l’installation finale fonctionnerait sans heurts dès le premier jour. Cette approche lui a permis non seulement d’améliorer l’efficience opérationnelle de son usine, mais aussi de réduire les risques et d’accélérer la mise sur le marché de ses produits, ce qui a apporté des avantages importants à l’entreprise et à ses clients.
Des technologies émergentes qui peuvent faire une énorme différence
En intégrant dans leurs processus de production des technologies numériques-clés telles que l’informatique dématérialisée, l’IA, le métavers industriel et l’analyse des mégadonnées (big data), les entreprises industrielles de toute taille peuvent accroître leur efficience, réduire les coûts et raccourcir les cycles de production grâce au suivi en temps réel et à la prise de décision automatisée, améliorant ainsi leurs capacités de fabrication.
L’impact de l’informatique dématérialisée
Les progrès réalisés dans le domaine de l’informatique dématérialisée offrent au secteur manufacturier des solutions évolutives et rentables qui améliorent l’efficience opérationnelle. En permettant un partage des données et une intégration fluides entre les différents services et sites, cette technologie facilite la collaboration.
Ses avantages sont importants pour les entreprises de toute taille. Ils le sont encore plus pour les petites et moyennes entreprises (PME), car ils démocratisent l’accès aux outils de fabrication avancés permettant la création de jumeaux numériques et la mise en place de continuités numériques. Le coût total de possession des logiciels est abaissé grâce à une réduction maximale des dépenses initiales et des coûts de maintenance et de mise à jour. Les PME peuvent utiliser l’informatique dématérialisée pour tirer parti des outils de fabrication numérique sans avoir à investir des sommes importantes dans leur infrastructure informatique. Cette accessibilité leur permet de mettre en œuvre des stratégies de transformation numérique dont le coût était peut-être trop élevé pour elles auparavant, ce qui les réservait aux grandes entreprises.
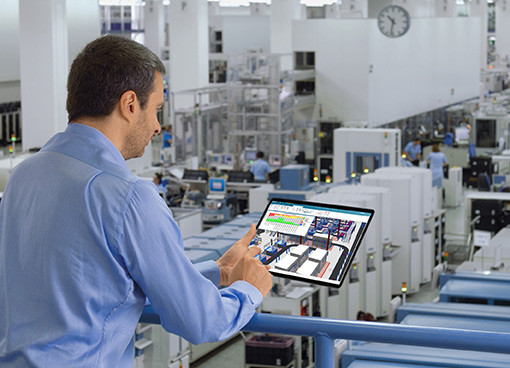
Globalement, on peut dire que l’informatique dématérialisée est un facilitateur. En adoptant des solutions basées sur le cloud, les industriels de toute taille peuvent gagner en flexibilité et en agilité, et ainsi s’adapter rapidement aux changements du marché et à l’évolution des exigences des clients, tout en se positionnant pour réussir dans un secteur qui évolue rapidement. En outre, le cloud permet d’utiliser des applications d’IA et d’apprentissage automatique (ML), qui peuvent optimiser les opérations de fabrication et améliorer la qualité des produits, et de mettre en œuvre le calcul hautes performances (HPC) pour travailler beaucoup plus vite.
Exploiter l’IA industrielle
Les progrès de l’IA permettent aux industriels d’analyser les vastes quantités de données qu’ils recueillent dans leurs usines et d’en extraire des informations précieuses qui peuvent les aider à accroître leur efficience et à réduire les erreurs. Basés sur l’IA, les copilotes peuvent également automatiser des tâches complexes, libérant ainsi des ressources et du personnel précieux, ou transformer des documents complexes en processus exploitables afin d’accélérer les opérations et de réduire au maximum les erreurs. Par exemple, dans la continuité numérique de fabrication de pièces présentée à la figure 1, l’IA est utilisée pour la conception générative de pièces imprimées en 3D et pour programmer automatiquement les machines-outils à commande numérique en vue d’un usinage des composants complexes basé sur les entités. Cela permet à des utilisateurs non spécialistes d’effectuer des tâches requérant les connaissances d’un expert, et ce sans avoir besoin d’une formation avancée ou de posséder des années d’expérience.
Avec l’IA, les industriels peuvent mieux utiliser leurs jumeaux numériques pour prévoir les besoins de maintenance, réduire les temps d’arrêt et prolonger la durée de vie de leurs équipements. Cela peut les aider à atteindre leurs objectifs de productivité et d’écoresponsabilité. L’IA peut également les aider à prendre des décisions éclairées concernant l’utilisation des ressources, en veillant à ce que les matières premières soient utilisées de manière efficiente et rentable.
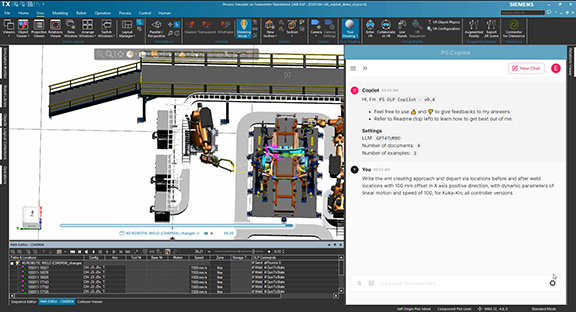
En résumé, l’IA peut offrir des avantages importants aux industriels tout en contribuant à faciliter leur transformation numérique.
En outre, l’IA et le cloud joueront un rôle essentiel dans le développement et l’utilisation de technologies et de techniques de fabrication innovantes, telles que le métavers industriel.
Les promesses du métavers industriel
Le métavers industriel constitue une évolution qui rassemble toutes les technologies numériques évoquées dans cet article afin de transformer l’avenir de la fabrication. Il s’appuie sur les jumeaux numériques complets du produit et de la production, combinés aux informations provenant des dispositifs Edge et des capteurs IoT, pour offrir un environnement numérique cohésif basé sur la physique, qui reflète le monde réel et peut être surveillé et ajusté en temps réel.
Offrant des outils améliorés de visualisation, de collaboration et de prise de décision et exploitant les processeurs graphiques (GPU) avancés et l’IA, le métavers industriel a le potentiel de révolutionner l’industrie. Il permet aux entreprises de travailler dans le monde numérique comme s’il était réel, et donc d’anticiper les problèmes potentiels et d’optimiser les opérations avant que la production physique ne commence, réduisant ainsi considérablement les coûts et améliorant l’efficience.
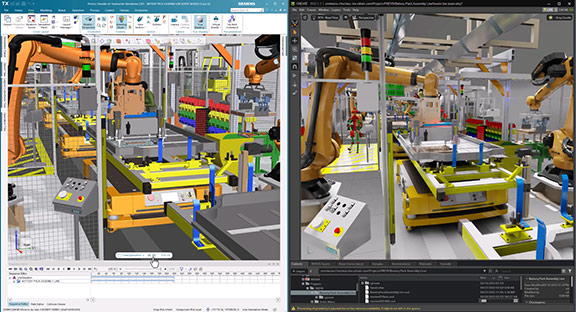
Cet espace numérique immersif sera rendu possible par le cloud, qui fournit l’infrastructure dont les entreprises ont besoin pour stocker et traiter les quantités massives de données générées par le métavers. Le cloud facilite également la collaboration en permettant aux différents services et écosystèmes de partager leurs données.
Siemens travaille avec des entreprises tournées vers l’avenir – telles que FREYR, un producteur norvégien de batteries propres – pour montrer comment le métavers industriel pourra aider les industriels à travailler et à collaborer.
À mesure que les entreprises adopteront cette technologie, exploiter la continuité numérique et créer des jumeaux numériques détaillés des installations de fabrication deviendra une pratique courante. Les industriels bénéficieront d’une meilleure collaboration et d’une meilleure prise de décision, d’une mise sur le marché plus rapide, de produits de meilleure qualité et de méthodes de fabrication plus écoresponsables.
L’avenir du secteur manufacturier
La transformation numérique de la fabrication n’est pas qu’une tendance, c’est un changement fondamental qui est en train de remodeler l’ensemble du secteur manufacturier. En adoptant la numérisation, les industriels peuvent fédérer les données, l’informatique dématérialisée, l’intelligence artificielle et le métavers industriel pour réduire les dépenses opérationnelles, augmenter la production et accroître les profits. Cette approche les aide à atteindre des niveaux d’efficience et de productivité sans précédent. Non seulement ce changement promet une agilité et une résilience plus grandes dans domaine de la fabrication, mais il ouvre aussi la voie à des prix compétitifs et à des pratiques écoresponsables, assurant ainsi un avenir solide à l’industrie mondiale.
À propos de l’auteur :
Zvi Feuer est vice-président senior de la division Digital Manufacturing Software de Siemens Digital Industries Software, une unité commerciale de Siemens Digital Industries. Digital Manufacturing Software développe des logiciels afin de fournir des solutions de classe mondiale pour la planification, la simulation et la validation de la fabrication (pièces et assemblages) et pour les opérations (MES, ordonnancement, qualité et automatisation).
Dans le cadre de ses fonctions actuelles, il est chargé de diriger des équipes et des projets mondiaux afin de développer et servir une base de clientèle mondiale en lui fournissant des solutions logicielles de fabrication numérique qui vont de l’optimisation des installations de production et de service jusqu’à la conception de chaînes d’assemblage, au développement et à la validation de systèmes de production, en passant par la programmation de machines à commande numérique pour la gestion de chaînes de production et d’usines.
Zvi Feuer a plus de 35 ans d’expérience dans le domaine de la gestion des logiciels destinés aux entreprises, et plus particulièrement celles du secteur manufacturier.