Les applications de jumeaux numériques de processus industriels gagnent du terrain. La technologie promet une exploitation optimale des usines tout au long de leur cycle de vie. C’est en tout cas la vision de Philippe Delespierre, Account Executive chez Hexagon France.
A travers l’acquisition en 2010 de la société Intergraph, le groupe suédois Hexagon s’intéresse plus que jamais au monde du process industriel. Pétrochimie, pharmaceutique, agroalimentaire, traitement des eaux usées… sont autant de domaines où le jumeau numérique des installations peut en effet trouver des applications. « Il s’agit de couvrir à la fois les phases d’ingénierie et d’exploitation tout au long de leur cycle de vie. Avec une notion de tel que construit intégrée au digital twin » explique Philippe Delespierre, Account Executive chez Hexagon France.
S’intéresser à ce qui est critique
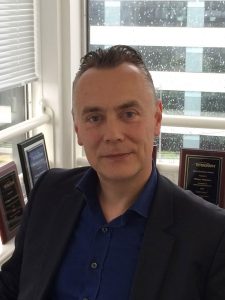
La vision d’Hexagon du jumeau numérique de telles installations est claire : se doter d’une seule plateforme de données pour toute la durée de vie de l’usine, capable de structurer des documents parfois anciens et d’offrir différentes vues aux métiers afférents. Et le groupe suédois a en effet dans son portefeuille de solutions de quoi couvrir la conception, la construction, l’exploitation et la sécurité des usines. « La digitalisation des process répond à trois besoins majeurs. En premier, éviter les silos de données. Chaque information doit être validée et bénéficier d’une procédure systématique. Et pour les sites sensibles, il est crucial d’avoir des documents à jour en cas de problème. En second, favoriser la mobilité pour accéder de partout aux systèmes d’information de l’entreprise. Il s’agit de gagner du temps, des ressources et d’optimiser par exemple les rondes d’inspection en évitant les documents papiers souvent inefficaces. Enfin, faciliter la gestion des alarmes, dont plus des 2/3 ne méritent pas l’attention. La digitalisation permet de structurer ces informations, de les connecter à leur environnement et de prioriser les actions à mener en fonction des alertes. Ceci exige d’intégrer les disciplines et les métiers avec des règles permettant de gérer efficacement les données ».
La construction du jumeau numérique ne repose pas seulement sur un aspect numérique. De nombreux points connexes doivent être pris en compte. La très classique résistance au changement nécessite d’impliquer les personnels concernés par la démarche. « Les opérateurs qui passent beaucoup de temps à ressaisir des données dans les systèmes GMAO, par exemple, vont en gagner et fournir une information plus riche grâce à l’utilisation de tablette lors de leurs inspections sur le site. Mais il faut leur adhésion au système. Par ailleurs, il est indispensable de définir des priorités pour éviter tout effet tunnel de projets trop ambitieux. Il vaut mieux avancer pas à pas et cibler les points où la digitalisation amènera un gain rapide, donc l’adhésion de petits groupes tout aussi rapidement. »
Les industriels sont aujourd’hui en mesure d’opérer des jumeaux numériques temps réel de leurs installations. « Un outil comme SDX pour le digital twin gère des liens entre des Tags, des localisations et des documents afférents. Ces liens permettent de voir à tout moment une citerne, par exemple, de naviguer depuis son smartphone dans son modèle 3D, de découvrir qu’une demande de modification y est attachée, et de consulter tous les documents techniques qui lui sont liés. Pour l’industriel, c’est la garantie d’avoir des informations à jour, exhaustives, si nécessaire temps réel, et les liens entre toutes les entités de son usine. »