Aujourd’hui, les constructeurs de machines industrielles sont confrontés à un marché volatile, ce qui les oblige à adopter de nouvelles approches pour développer la prochaine génération de produits. Comme toujours, ils subissent les pressions permanentes concernant la qualité, le coût et les performances. En outre, les exigences en matière d’écoresponsabilité sont désormais au premier plan. L’accent est mis sur les économies d’énergie, sur la réduction des émissions de carbone et sur la diminution de la quantité de rebuts et de déchets.
De plus, les grandes tendances mondiales ont un impact sur les industriels du monde entier. Parallèlement, les changements socio-politiques entraînent une évolution des modèles économiques, avec notamment la relocalisation et la servitisation. Quant au secteur, il évolue également, avec l’arrivée de nouveaux acteurs. Mais les industriels opérant dans des domaines bien établis voient également des opportunités dans les domaines émergents et en profitent pour s’étendre à des marchés adjacents ou nouveaux. Par exemple, les constructeurs de machines pour l’industrie du papier ou du verre se lancent dans le développement de machines de fabrication de batteries afin de répondre à la forte augmentation de la demande de véhicules électriques. Toutefois, la pénurie de main-d’œuvre – dont souffrent autant les constructeurs de machines que le secteur manufacturier – accroît le besoin d’automatisation. L’usine du futur se développe maintenant autour de trois paradigmes : le développement durable, la flexibilité et la main-d’œuvre de demain.
Les avancées techniques offrent aux industriels des opportunités de prospérer malgré la myriade de défis auxquels ils sont confrontés. Ces avancées sont rendues possibles par la profusion de données et une meilleure compréhension de celles-ci, qui sont le fruit de la numérisation. En effet, cette dernière intègre les outils numériques, les systèmes et les données IoT, connectant ainsi des informations issues des domaines de la conception, de l’ingénierie, de la production et de la maintenance et qui étaient auparavant cloisonnées.
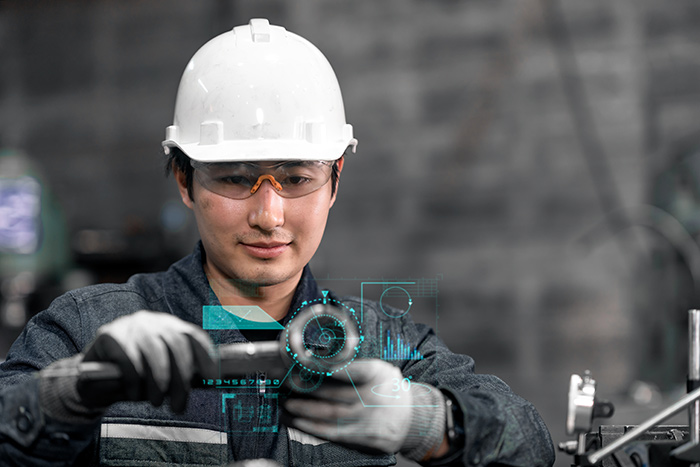
Grâce à la numérisation, les industriels peuvent aller au-delà de l’automatisation et mettre en place des environnements de production plus prédictifs et plus adaptatifs. La souplesse de la fabrication adaptative permet d’ajuster aisément la production à l’évolution du marché et des besoins des clients. En outre, elle simplifie les flux de travail pour que les industriels puissent en faire plus avec la même main-d’œuvre.
La numérisation réduit également les risques liés à la fabrication, en instaurant des processus plus souples et en permettant d’accéder à des données cruciales dans l’ensemble des nombreuses disciplines d’ingénierie et de production. La combinaison des données provenant de toutes ces disciplines autrefois cloisonnées nécessite des solutions reposant sur une compréhension approfondie de la conception des machines, de la simulation, de l’automatisation des usines et de la gestion du cycle de vie des produits (PLM).
Le jumeau numérique : au cœur de la numérisation
Cette renaissance dans le secteur manufacturier passe par la numérisation de l’ensemble du processus de production, y compris les machines utilisées ; et cela commence dès la conception par la création du jumeau numérique de la machine intelligente. Tout au long du processus de conception, le jumeau numérique de la machine est développé grâce à une ingénierie multidisciplinaire qui englobe les systèmes mécaniques, logiciels, électriques et d’automatisation de la machine. Ce jumeau numérique est initialement utilisé pour l’étude et l’évaluation de la conception dans le cadre du prototypage virtuel. Lorsque la machine est prête à être mise en œuvre, son jumeau numérique permet de procéder à une mise en service virtuelle avant que la machine ne soit physiquement installée, ce qui permet de se familiariser avec la machine et de former son opérateur, réduisant ainsi considérablement les risques et le temps nécessaire à la mise en service.
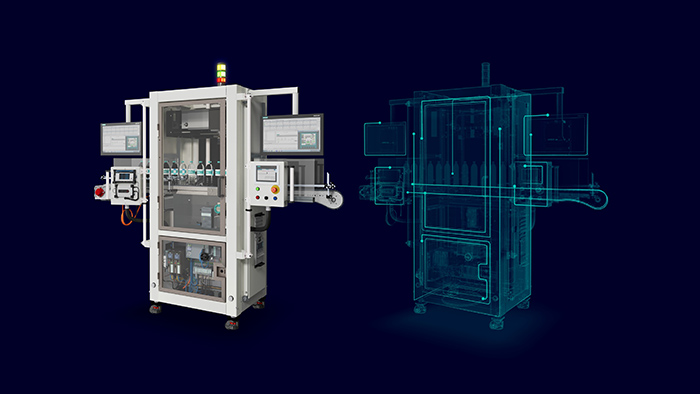
Une fois la machine installée dans l’usine, son jumeau numérique est continuellement enrichi avec les données générées lors de l’exploitation de la machine tout au long de sa durée de vie. Cet avantage précieux permet de créer une boucle fermée entre la représentation réelle et la représentation numérique. D’une fidélité croissante, ce jumeau numérique opérationnel fournit des informations inestimables sur le fonctionnement de la machine, permettant à l’équipe de production de surveiller et d’améliorer en permanence l’efficience et la qualité de la fabrication. Le jumeau numérique accroît aussi la fiabilité opérationnelle. En effet, il améliore la gestion de la maintenance en fournissant des données et des informations concrètes sur le moment où une machine a besoin d’être entretenue, ce qui contribue à éviter les temps d’arrêt imprévus ou les dommages à la machine. Il peut également accélérer le lancement de nouveaux produits, en permettant à l’équipe de production de tester les nouveaux processus envisagés avant de procéder aux modifications physiques correspondantes dans l’usine.
Transformer la production grâce à la continuité numérique
Une fois mise en œuvre, la numérisation ouvre de nouveaux horizons pour la production. Des jumeaux numériques solides de machines discrètes peuvent s’intégrer dans une continuité numérique s’étendant de ces machines à l’agencement et à la conception de l’usine, puis aux opérations de fabrication. La simulation au niveau de l’usine permet de simuler l’ensemble des machines, des processus d’automatisation et des lignes de production, et ainsi d’optimiser en permanence la vitesse et la qualité. Les industriels peuvent optimiser les performances globales de l’usine, en s’intéressant d’abord à la planification puis à la production. Le résultat est une usine intelligente où les données sont accessibles et partagées de manière fluide tout au long de la production.
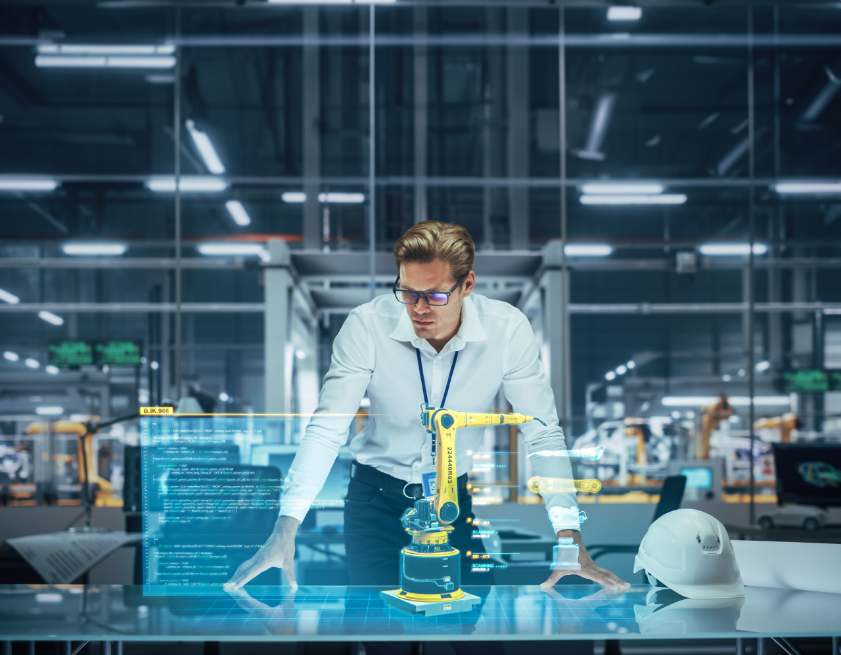
La numérisation offre des avantages importants face à des problématiques telles que l’écoresponsabilité, la flexibilité de la production et les pénuries de main-d’œuvre :
- Écoresponsabilité grâce à la gestion de l’énergie – Les industriels peuvent en toute confiance procéder à une évaluation complète de la consommation énergétique de leurs usines, à son optimisation et à la réduction des émissions de CO2, et rédiger un rapport d’évaluation pour une usine particulière ou l’ensemble de leurs sites.
- Flexibilité de la production – Une véritable convergence IT/OT est possible, qui permet de connecter et analyser les données dans l’ensemble de la chaîne d’approvisionnement, des opérations de production et des processus métier, et ainsi de prendre en temps quasi réel des décisions basées sur les données.
- Mise en œuvre de la collaboration homme-machine avec l’intelligence artificielle/l’apprentissage machine et l’analyse des données, y compris les données provenant de puissantes fonctionnalités Edge industrielles. L’accès à de meilleures informations permet de réagir rapidement aux événements imprévus. En outre, l’utilisation de l’IA générative pour l’analyse opérationnelle (par exemple, Siemens Industrial Copilot) permettra aux utilisateurs de générer, optimiser et déboguer rapidement un code d’automatisation complexe, et de réduire considérablement la durée des simulations. Une tâche qui prenait auparavant des semaines ne prendra alors plus que quelques minutes.
En outre, l’instauration d’une continuité numérique réduit considérablement les risques lors de la conversion ou de la modification de la ligne de production pour s’adapter aux fluctuations du marché. Toutefois, alors que nous continuons à relier le monde physique au monde numérique, la cybersécurité doit être une priorité et être intégrée dans chaque étape de la numérisation. En effet, la complexité des risques et des menaces ne cesse de croître, et ces dernières s’étendent à des espaces numériques et géographiques toujours plus vastes. Garantir la cybersécurité des données et des produits n’a donc jamais été aussi important.
Commencer modestement et évoluer intelligemment
Malgré tous les avantages offerts par la numérisation, il peut être intimidant de faire le premier pas. La question que me posent nos clients industriels est la suivante : « Par où commencer ? » La bonne nouvelle, c’est qu’ils peuvent commencer à petite échelle, puis évoluer lorsqu’ils sont prêts. L’arrivée récente de solutions de cloud industriel spécialement conçues pour les constructeurs de machines et les industriels rend les choses plus faciles que jamais. Ces solutions sont parfaitement adaptées aux marchés et régions émergents ainsi qu’à la relocalisation.
Chez Siemens, nous avons défini les cinq étapes de la maturité numérique (figure 1) pour aider les clients à déterminer par où commencer. Tout d’abord, nous procédons à une évaluation de la maturité numérique du client pour savoir où il se situe dans ce continuum. Ensuite, nous étudions ce que les leaders du même secteur d’activité ont mis en œuvre avec succès. L’étape suivante consiste à créer une feuille de route pour le client, afin de lui permettre de faire entrer son processus de production dans une ère nouvelle.
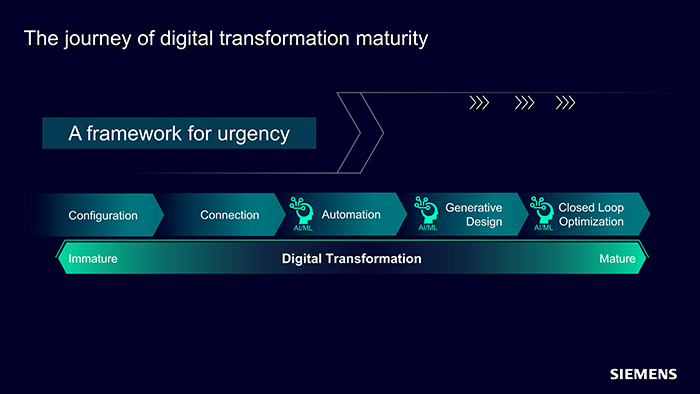
Aujourd’hui, la plupart des constructeurs de machines ont franchi les deux premières étapes de ce processus de maturation. Ces étapes sont la configuration, c’est-à-dire le passage d’un cadre de données basé sur des documents à un cadre de données basé sur des modèles, et la connexion, qui encourage le décloisonnement des domaines pour permettre le partage des données. Ces deux étapes améliorent nettement la traçabilité et l’accessibilité des données dans l’ensemble de l’entreprise, ce qui permet d’augmenter l’efficience des processus, d’accroître la flexibilité de l’ingénierie et d’améliorer les résultats, même pour les projets aux délais très serrés. Toutefois, pour tirer pleinement parti de la numérisation, les constructeurs de machines incluent désormais l’automatisation dans leurs pratiques de conception, ce qui conduit à des niveaux plus élevés de conception générative et, à terme, à l’optimisation en boucle fermée.
Par exemple, la société norvégienne Tronrud Engineering construit et fournit des machines d’emballage flexibles et innovantes à des clients nationaux et internationaux. Forte de plus de 40 ans d’expérience, l’entreprise a fourni des solutions d’emballage secondaire dans le monde entier et a optimisé une machine d’emballage de nouvelle génération qui emballe des « pillow bags » (sacs moletonnés) dans des boîtes. Avec l’aide de Siemens, notamment pour la création d’un jumeau numérique, ils ont obtenu des résultats impressionnants :
« Nous avons réduit la phase de conception d’environ 10 % et la phase de mise en service de 20 à 25 % », a déclaré Tor Morten Stadum, responsable PLM chez Tronrud Engineering.
Commencez dès maintenant votre parcours de transformation
Grâce à la numérisation, les constructeurs de machines peuvent s’engager en toute confiance dans un avenir innovant. Ils peuvent passer de l’automatisation à la fabrication adaptative et mettre en place une continuité numérique dans l’ensemble de leurs opérations. Cette transformation les aidera à prospérer dans l’environnement dynamique actuel, en s’adaptant aux changements imprévus que réserve cette époque de renaissance passionnante pour le secteur manufacturier.
___
À propos de l’auteur :
Rahul Garg est le vice-président responsable de la division Constructions mécaniques et du secteur des PME chez Siemens Digital Industries Software. Il est chargé de définir et mettre en œuvre des initiatives et des solutions stratégiques clés et d’assurer le développement commercial international. Avec son équipe, il a pour mission d’identifier les initiatives stratégiques requises, de développer des solutions pour le secteur industriel en étroite collaboration avec des entreprises clientes leaders, et d’assurer un leadership intellectuel sur les nouveaux problèmes auxquels le secteur est confronté. Son expérience et ses compétences sont le fruit de 25 ans de carrière dans le domaine de la fourniture, au secteur manufacturier mondial, de solutions logicielles favorisant l’innovation en matière d’ingénierie et de fabrication de produits. Il a travaillé dans la recherche et le développement mais a aussi occupé des postes de direction dans les domaines des programmes, des ventes et de la gestion des pertes et profits. Depuis 2007, il s’est spécialisé dans le secteur des constructions mécaniques et des équipements lourds.